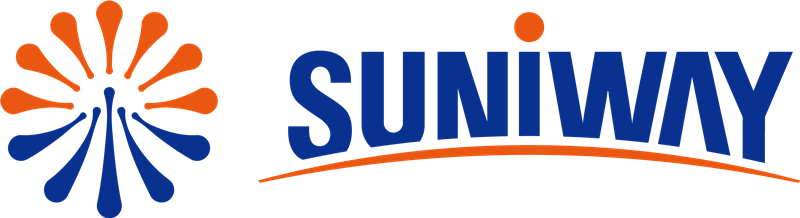
Upgrade to High-Speed Internet for only ₱1499/month!
Enjoy up to 100 Mbps fiber broadband, perfect for browsing, streaming, and gaming.
Visit Suniway.ph to learn
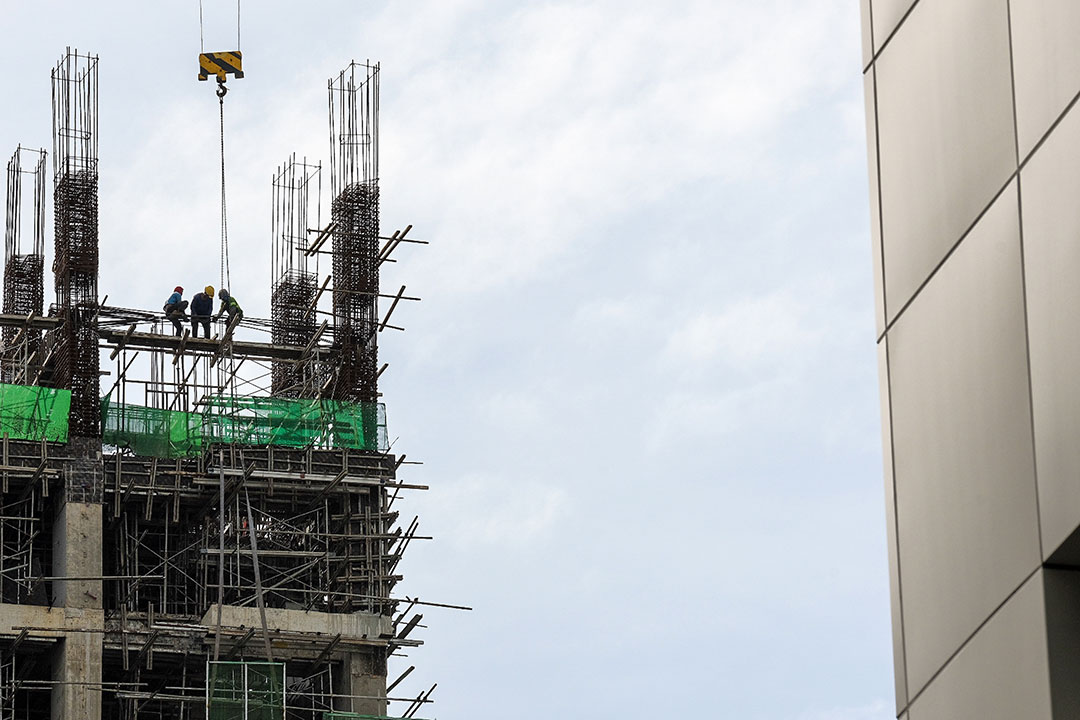
By Beatriz Marie D. Cruz, Reporter
THE COST of building materials is likely to remain steady this year amid government demand and slowing inflation, although geopolitical uncertainties may cause price volatility, according to construction company executives.
“Based on the current market situation, we see a steady trend in prices, with partial bias for marginal increases due to demand coming from government infrastructure projects as well as the rollout of economic and socialized housing projects,” Megawide Construction Corp. said in an e-mail to BusinessWorld.
Jason C. Valderrama, president and chief executive officer at construction firm JCV & Associates, said prices of construction materials are expected to remain stable amid cooling inflation and easing interest rates.
“The inflation rate has been the lowest in the last five years and the construction materials wholesale price index moves in lock step with it, so prices of construction materials will be stable this year,” he said in an e-mail.
In the first three months of the year, the wholesale price growth of construction materials in Metro Manila averaged 0.1%, lower than 1.1% a year ago, latest data from the Philippine Statistics Authority showed.
Headline inflation averaged 2.2% in the January-to-March period, within the central bank’s 2-4% target.
Mr. Valderrama said the resumption of the Bangko Sentral ng Pilipinas’ (BSP) easing cycle would further temper inflation and stabilize construction material prices.
The BSP on April 10 cut rates by 25 basis points, bringing its key policy rate to 5.5%. BSP Governor Eli M. Remolona, Jr. said further rate cuts will likely be delivered in “baby steps” or in 25-bp increments.
“The Philippines is always reliant on developments in the global commodity markets like oil, steel products and China’s economic situation/trends, and basic construction materials like cement, pipes and lumber may be very volatile,” Aboitiz Construction Vice-President for Strategic Asset and Supply Chain Management Eric King said in an e-mail to BusinessWorld.
However, the price and supply of raw steel are expected to remain steady through 2025, he said.
“We anticipate that this will result in a stable availability and unchanged base cost of our steel base materials, including steel fibers, dowel cradles, armor joints, gabions, and other double-twist items.”
The expected slowdown of global oil prices would also stabilize the cost of energy intensive materials like steel and cement, according to Megawide Construction.
“As of the latest forecasts, oil prices are expected to slow down on account of higher output coupled with reduced demand,” Megawide Construction said.
The Organization of the Petroleum Exporting Countries on April 14 reduced its 2025 global oil demand growth forecast as the United States’ tariff policy has dampened economic activity, Reuters reported.
“This scenario, however, can change depending on the intensity of the ongoing trade war triggered by US policy directions,” Megawide said.
IMPACT OF TRADE WAR
However, the US tariff policy as well as ongoing conflicts in the Middle East could still hurt global supply chains, affecting the cost of building materials.
“If the current state of tensions in Europe, the Middle East and Asia worsens, shipping routes may be affected and cause higher transport and landed costs. In addition, the trade war could disrupt traditional sourcing channels and impact pricing, which should also be reflected in prices,” the company said.
US President Donald J. Trump on April 9 announced a 90-day suspension of reciprocal tariffs with its trading partners except China, although the baseline 10% tariff on most US imports remained in effect.
Philippine exports were imposed a 17% reciprocal tariff by the US, the second- lowest among Southeast Asian countries.
Cebu Landmasters, Inc. Chief Operating Officer Jose Franco B. Soberano said the company is still seeing “very favorable” steel prices and stable cement prices amid tariff pressures.
“It might even be beneficial to us because there will be more supply coming to our region… We will get more competitive and aggressive pricing from Southeast Asia or Asian countries that supply construction materials to us. Costs have gone up in the last three years due to the supply chain disruptions and the pandemic, but it’s become more stable now,” Mr. Soberano said in an interview aired on Money Talks with Cathy Yang on One News last week.
However, Mr. Soberano said that while the company is taking advantage of pricing opportunities, it is “not locking in anything beyond three or six months.”
Mr. Valderrama said he expects muted US demand for construction materials from China and other countries due to the trade war. He noted these countries will look to send more of their products to other export markets such as the Philippines.
“There will be a lot of available supply from China when it comes to steel, so if there is nowhere to go because of the tariff issue, then the tendency is there will be supply available [for the Philippines],” PHINMA Corp. Director and Executive Vice-President for the Construction Materials Group Eduardo A. Sahagun said via telephone.
To navigate unexpected changes in the market, Mr. King said Philippine companies should foster strong relationships with its business partners and suppliers.
“In some advanced organizations and industries, they have started to use data and AI-powered tools to help them find better prices and manage their inventory more efficiently,” he said.